The incident in question involved the amputation of a worker's finger while operating a packaging machine. The company, which has not been named, has been fined $147,000 by the Occupational Safety and Health Administration (OSHA) for failing to properly train its employees on the safe operation of the machinery, and for not providing adequate protective equipment.
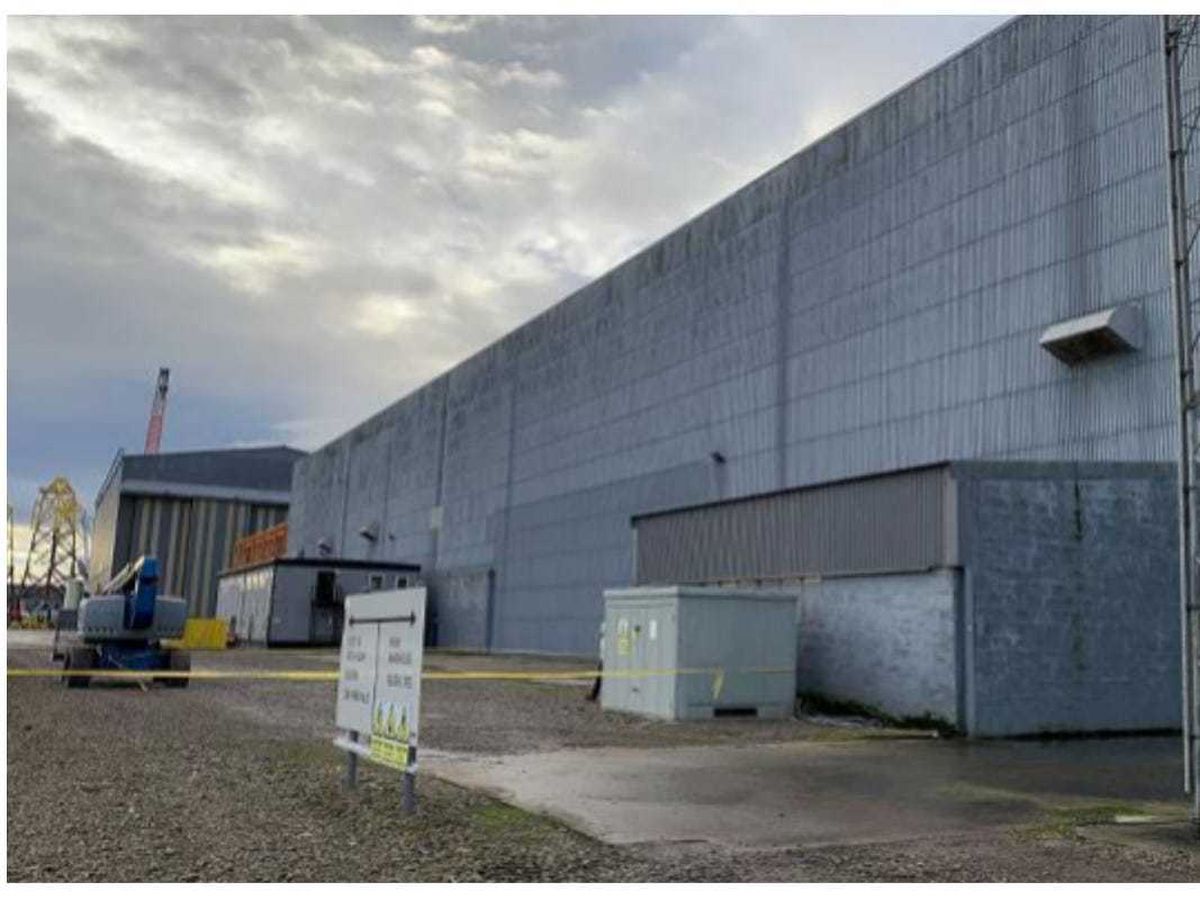
Sadly, this incident is not an isolated one. In fact, less than six months prior to the amputation accident, OSHA had cited the same company for similar hazards in a separate investigation. This begs the question -- why do some companies continue to put their workers at risk?
It's no secret that the manufacturing industry can be a dangerous one. There are countless hazards present in any production facility, from heavy machinery to dangerous chemicals. That's why it's so important for companies to take workplace safety seriously. Unfortunately, for some companies, the motivation to prioritize safety just isn't there.
Some companies may believe that cutting corners when it comes to safety measures will save them money in the short term. They may believe that the cost of training employees or providing protective equipment is too high, and that the risk of an accident is low. However, this line of thinking is incredibly short-sighted.
Firstly, accidents can be incredibly costly for companies. Injuries can result in expensive lawsuits, workers' compensation claims, and increased insurance costs. Additionally, accidents can lead to lost productivity, as workers may need time off to recover from injuries. It's simply not worth the risk to neglect workplace safety measures.
Secondly, there's the human cost to consider. Injuries sustained on the job can be life-altering for workers and their families. No amount of money saved on safety measures is worth the health and wellbeing of employees.
So, what can companies do to prioritize workplace safety in the manufacturing of spices and related products? Here are a few key steps that every company should take:
1. Conduct regular safety training
It's not enough to assume that employees know how to operate machinery safely or handle hazardous materials. Companies should make regular safety training a priority, ensuring that workers are aware of potential hazards and know how to mitigate them.
2. Provide personal protective equipment (PPE)
Whether it's masks, gloves, or safety glasses, companies must ensure that their workers have the proper PPE for the job. Ensuring that employees have access to the right equipment can help prevent accidents and injuries.
3. Conduct regular safety audits
It can be easy for hazards to go unnoticed in a busy production facility. Regular safety audits can help identify potential issues and allow for preventative measures to be taken.
4. Encourage employees to speak out
Workers may have insights into potential safety hazards that management is unaware of. Encouraging employees to speak out about potential issues can help prevent accidents and promote a culture of safety in the workplace.
Ultimately, companies in the spice manufacturing industry need to make safety a priority. By doing so, they can protect their workers, avoid costly accidents, and ensure the long-term success of their business.